IMPULS
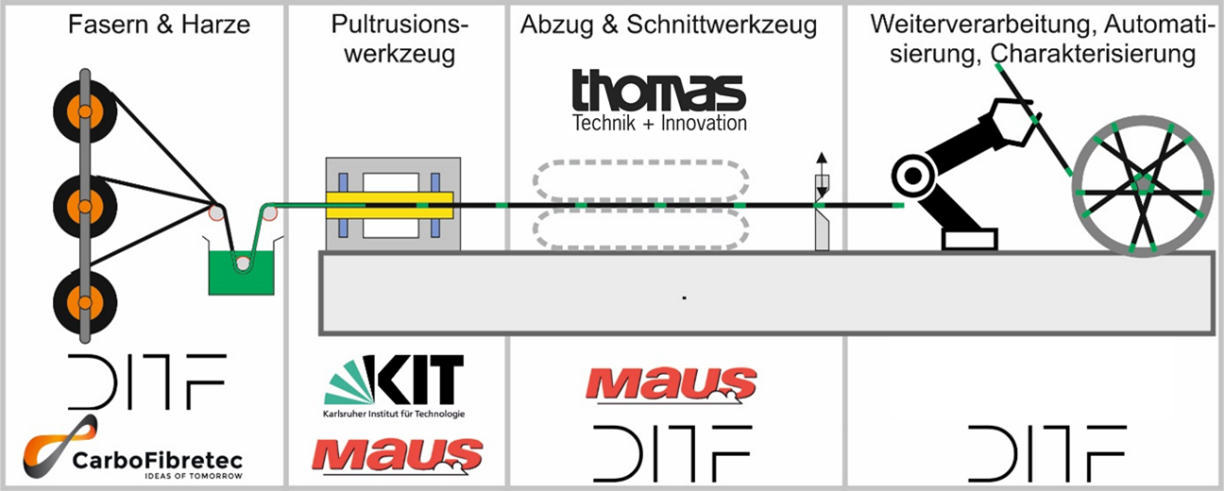
The fiber composite industry is one of the fastest growing industry sectors worldwide. The main reason for this is the high stiffness and strength combined with low weight, which enables weight savings of up to 60% and 25% respectively compared with classic materials such as steel and aluminum. The main obstacle to the widespread use of fiber composite components is the high cost of most manufacturing processes. The pultrusion process is an exception to this rule, as it enables continuous production of fiber composite profiles at process speeds of up to 5 m per minute. In this process, fibers, which are impregnated with a thermoset or thermoplastic matrix, are drawn through a heated mold. A thermoset matrix hardens as it passes through the heated mold, while a thermoplastic matrix initially melts in the mold and then solidifies in a subsequent cooling segment.
Microwave-heated pultrusion promises several advantages over the conventional process. Whereas in the conventional pultrusion process the profile is heated indirectly via the mold, in microwave-assisted pultrusion the profile is heated directly by volumetric means, which enables a much more targeted and thus more efficient energy input. In addition, the heating rate is not limited by the thermal conductivity of the mold and profile, but only by the available microwave power. As a result, higher pull speeds can be achieved with a shorter mold length. The main advantage of microwave heating, however, is that by directly heating the profile in the cold mold, the curing process can be temporarily interrupted. The resulting uncured areas can be reshaped and cured in a subsequent step. This opens up a wide range of new applications, such as trusses for crane booms.
The aim of the IMPULS project is to develop a microwave pultrusion system for the sequential curing of carbon fiber profiles, with particular emphasis on achieving the sharpest possible transitions between the cured and uncured areas.
Projectpartner:
Deutsche Institute für Textil- und Faserforschung Denkendorf (DITF)
Maus GmbH Modell- und Formenbau
Thomas GmbH + Co. Technik + Innovation KG
Funding: ZF4204604 BL8
Duration: 2018 - 2022