Surface modification of materials using pulsed electron beams
Using intensive pulsed electron beams, energy can be deposited into surface layers of materials very efficiently and fast. Material surfaces are melted with a single pulse to a depth of up to 100 µm depending on the specific energy input (5-60 J/cm²). After termination of the pulse (some 10 µs) the melt layer cools by heat conduction with cooling rates of 106-109 K/s. Thereby, micro-crystalline, nano-crystalline or even amorphous structures in the modified surface layer are formed that show improved hardness, corrosion resistance and wear resistance. Currently, the most important application is surface alloying of metals with different materials. The alloying of aluminum into steel surfaces for improved corrosion resistance is in the focus of the application related work.
Pulsed electron beams with large diameter and sufficient beam energy can be created using high voltage generators and vacuum diodes. As electron source a multipoint explosive emission cathode consisting of several carbon fibre bundles is used. Besides the very rapid quasi adiabatic melting of surfaces and the correlated high cooling rates, the major difference compared to other alternative processes such as e.g. Laser is the possible large treatment areas (some 100 cm²). The facilities GESA I, GESA II and GESA IV, which were built in close cooperation with the Efremov institute in St. Petersburg, deliver electron beam pulses with some tens of microseconds pulse duration and electron energies between 50 and 400 keV.
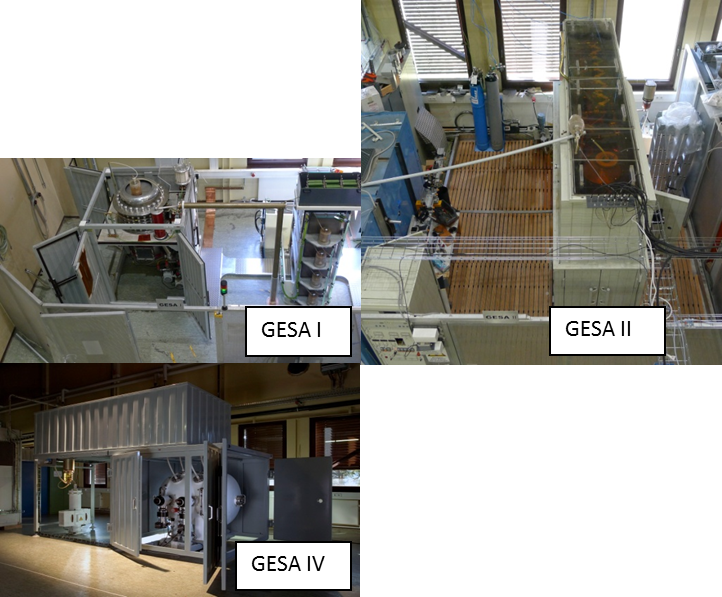
Working areas:
Material development for liquid metal systems
|
|
Surface alloying:
|
|
Corrosion tests:
The 8 COSTA (COrrosion in STAgnant lead alloys) test stands allow the exposure of more than 100 specimens at different temperatures (from 300 °C to 900 °C) and oxygen activities (from reducing to saturation conditions) simultaneously. Exposures up to 10,000 h controlled conditions have been realized so far. COSTA test-stands were also delivered to external research organizations (e.g. KTH - Stockholm). The CORELLA (CORrosion Erosion in Liquid Lead Alloys) facility is used to expose specimens to rotating liquid metal for the investigation of combined erosion / corrosion stability of materials. The FRETHME (FRETing corrosion in Heavy liquid Metals) facility is employed for fretting tests (wear at small sliding amplitudes) in liquid lead alloys. Three samples can be simultaneously tested at fixed amplitude with different loads. All relevant parameters such as liquid metal conditions (temperature and oxygen content), load, motion amplitude and friction force are recorded. . |
|
Liquid metal technology:
Setting-up and control of the oxygen content is one of the important issues for experiments and investigations in liquid metals. For this purpose a gas phase oxygen control system (OCS) was developed and used for all test facilities in our institute and at several other test facilities of internal and external partner associations. |
|
Experimental equipment for post investigations:
Metallographic equipment for sample preparation; diverse light optical microscopes; 2 SEM (Scanning electron microscopes) equipped with EDX (energy dispersive x-ray analysis) for elemental characterization; XRD (x-ray diffraction); Thermal balance combined with DTA (differential thermal analysis); Hardness tester; small scale specimen tensile and bending stage for SEM use; white light profilometer for topography; mass spectrometer; Furnaces for heat treatment and sintering experiments. High temperature applications:
In this area, surface modification by re-melting and alloying of different elements using pulsed electron beams aims to improve the properties of turbine plates; e.g. an improved adherence of thermal barrier coatings will lead to an increase in life-time.
Wear resistance Surface hardening by modifying the micro-structure using the GESA process improves the wear resistance of materials and machine parts such as gear wheels and tappets. Surface alloying or GESA re-melting of carburized surfaces are additional options to increase the hardness and the wear resistance. |
|
Electron beam physics and beam-target interaction High-speed cameras in streak and framing mode allow the in-situ observation of the surface melting process. Applying ultra short time spectroscopy, the state and properties of evaporated material close to the surface can be investigated. The results of in-situ analyses are combined together with simulations to understand and describe the physical processes during re-melting and cooling. |